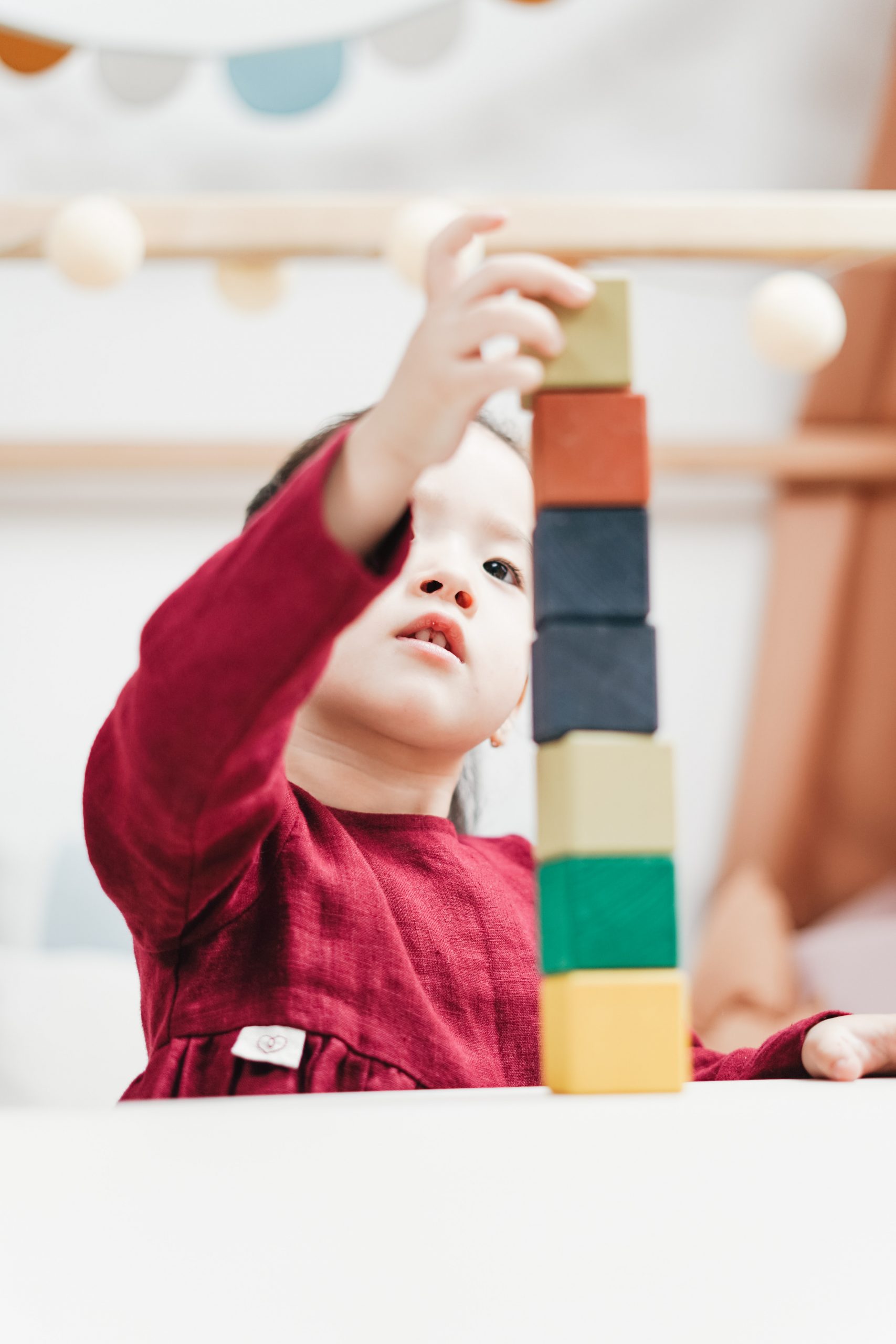
Reduce Time and Money on Construction
According to this great summary, 71.4% of construction firms that committed to using modular components saw a noticeable difference in Time to Market. In addition, “79% of General Contractors, 69% of Architects/Engineers, and 53% of Trade Contractors plan on utilizing a “relocatable modular structure” in at least one of their projects within the next three years.” It is no surprise that these demonstrated reductions in time spent on project, translates directly into significant savings on the construction project budget. For example, those modular construction projects that were able to achieve a 50% reduction in schedule showed an average cost reduction of $10.93/sqft.
Here is a listing of 7 great modular construction projects, from hospitals, to schools, to a marijuana dispensary. Some great examples of this construction modality.